Reducing Waste: Eco-Conscious Practices in Flexible PCB Manufacturing
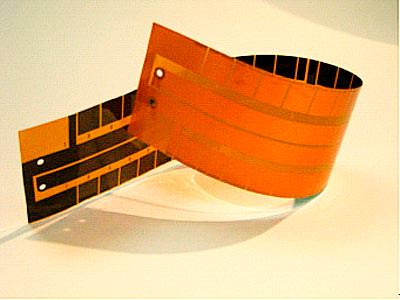
In the rapidly growing field of electronics, the demand for flexible printed circuit boards (PCBs) has soared. These lightweight, versatile components are integral to countless modern devices such as wearables, smartphones, and medical equipment. As the industry continues to expand, it becomes increasingly important to address the environmental impact of PCB manufacturing. Traditional PCB production processes often contribute to significant waste generation, but flexible PCB manufacturers are now exploring innovative and sustainable solutions. This blog will delve into eco-conscious practices that help reduce waste in the production of flexible PCBs, ensuring a greener future for the electronics industry.
The Environmental Impact of PCB Manufacturing
Traditional PCB manufacturing involves multiple steps, including material processing, etching, drilling, and surface treatment. Throughout this process, a considerable amount of waste is generated in the form of scrap materials, chemicals, and pollutants. In fact, it is estimated that a typical PCB manufacturing facility can generate up to 20% waste during the production cycle. With the growing environmental awareness across industries, reducing waste has become a critical concern for flexible PCB manufacturers. By embracing eco-conscious practices, manufacturers can reduce their environmental footprint while still producing high-quality, flexible PCBs.
1. Minimizing Material Waste with Precision Engineering
One of the primary ways to reduce waste in flexible PCB manufacturing is through precision engineering. By using advanced design techniques, manufacturers can optimize material usage, ensuring that every inch of the flexible PCB material is utilized effectively. This involves leveraging tools like CAD software to create efficient designs that minimize excess material. Additionally, precise cutting and routing methods can further reduce scrap, allowing manufacturers to maximize the yield from every sheet of flexible PCB material.
2. Recycling and Reusing Materials
Recycling is one of the most effective ways to reduce waste in flexible PCB manufacturing. Many components used in PCB production, such as copper and fiberglass, can be recycled and reused in future production cycles. Flexible PCB manufacturers are increasingly implementing closed-loop recycling systems where materials from old boards are collected, processed, and then used to produce new PCBs. This practice significantly reduces the need for virgin materials and decreases the amount of waste that ends up in landfills.
Beyond just recycling raw materials, manufacturers are also focusing on reusing other elements, such as packaging and equipment. For instance, packaging materials like cardboard, plastic wraps, and foam can be recycled or repurposed to reduce their environmental impact. You can find out more about the specific recycling techniques employed by eco-conscious manufacturers by researching their sustainability initiatives.
3. Reducing Chemical Waste through Safer Processes
The chemical treatments used in the PCB manufacturing process can generate harmful waste, including heavy metals and toxic solvents. However, many flexible PCB manufacturers are now adopting safer and more sustainable chemical processes. For example, water-based etching solutions are replacing hazardous acid-based chemicals, which not only reduces chemical waste but also improves the health and safety conditions within manufacturing facilities.
Moreover, manufacturers are increasingly using green chemistry principles to develop environmentally friendly alternatives for plating, cleaning, and surface treatments. These safer processes help minimize the environmental impact and ensure compliance with stringent regulatory standards. As the industry shifts towards more sustainable chemical processes, you can find out more about these practices by visiting company websites or industry reports that highlight eco-friendly PCB manufacturing methods.
4. Energy Efficiency in Manufacturing
Energy consumption is another significant aspect of reducing waste in flexible PCB manufacturing. Traditional manufacturing processes can be energy-intensive, contributing to both environmental harm and increased operational costs. To address this, many flexible PCB manufacturers are investing in energy-efficient technologies. For example, the use of LED lighting, automated machinery, and advanced heating and cooling systems can significantly reduce energy consumption.
In addition to reducing energy usage, manufacturers are also exploring renewable energy sources like solar or wind power to further minimize their carbon footprint. By incorporating energy-efficient systems and utilizing renewable energy, manufacturers not only cut down on waste but also contribute to a more sustainable, greener manufacturing process.
5. Sustainable Packaging Solutions
The packaging of flexible PCBs is another area where waste reduction can make a significant impact. Traditional packaging materials, such as plastic wraps and Styrofoam, are harmful to the environment and often end up in landfills. Eco-conscious flexible PCB manufacturers are now shifting towards sustainable packaging options, such as biodegradable materials, recycled cardboard, and reusable containers.
By opting for sustainable packaging, manufacturers can reduce waste during shipping and storage, contributing to a more environmentally responsible production process. Go right here to see how different manufacturers are adopting these eco-friendly packaging practices and making strides toward sustainability.
6. Collaboration and Industry Standards
Reducing waste is not a task that can be accomplished by individual manufacturers alone. It requires industry-wide collaboration and the establishment of common sustainability standards. Many flexible PCB manufacturers are now participating in global initiatives aimed at improving environmental responsibility within the electronics industry. Organizations such as the International Electronics Manufacturing Initiative (iNEMI) and the IPC are actively working to set guidelines and promote best practices for sustainable PCB manufacturing.
By adhering to these industry standards, manufacturers can ensure that their practices align with global sustainability goals, further reducing waste and environmental harm. Working together, companies can share knowledge, improve techniques, and drive innovation in eco-conscious manufacturing.
Conclusion
The demand for flexible PCBs is on the rise, but with this growth comes the responsibility to adopt eco-conscious practices that reduce waste and environmental impact. From precision engineering and recycling to safer chemical processes and energy efficiency, flexible PCB manufacturers are taking steps to make their operations more sustainable. By focusing on these eco-friendly practices, manufacturers can ensure that they contribute to a greener future while still delivering high-quality, reliable products.
As a consumer or business partner, it’s important to be aware of the sustainability efforts of your PCB suppliers. You can find out more about their eco-conscious practices by asking for detailed sustainability reports or by researching their commitment to reducing waste. Together, we can help make the electronics industry more sustainable and environmentally responsible.